Trades Shortage: How Can You Avoid Project Disruption?
A trades shortage means there's now a 20-year-high demand for builders, which could disrupt building projects
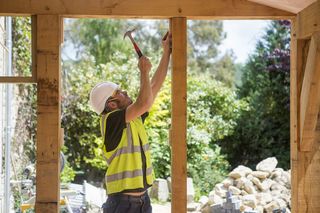
A trades shortages and depleting supplies of building materials means self builders and renovators will need to work further in advance to ensure their projects aren’t disrupted, industry experts have warned.
These are turbulent times if you’re in the midst of aself build, renovating orbuilding an extension. An ongoingconstruction materials shortagehas resulted in skyrocketing prices for certain materials, and this is set to continue for the rest of the year and possibly even into next year.
Furthermore, builders’ workloads are at their highest levels for 10 years according to a recent survey from the Federation of Master Builders (FMB). The impact of Brexit (delays to supply chains) and the pandemic (thousands of construction workers were ‘pinged’ to self-isolate in July) have exacerbated the situation further.
What this means for your project will depend on several factors, including your materials of choice, and how open your lines of communication are with your tradespeople.
How to Manage the Trades Shortage
Forward thinking is paramount, especially when it comes to ordering materials. “Self builders have to get their ducks in a row much further in advance than ever before,” says Nick Lloyd, managing director of sustainable building companyUrbane Eco(opens in new tab).
“Whereas lead times have previously been six weeks for materials, they’re now around 12 weeks. Our insulation products, for example, now need to be ordered several months in advance.”
Terry Huggett ofTerry Huggett Developments(opens in new tab), which specialises in self builds, renovations and restorations, says: “Consider your design and materials in advance. If you need unique products for your build then try to see where it is readily available.”
Another tip, Huggett adds, is to make sure you have enough space to store materials. If you’re ordering large supplies of plasterboard, for example, then you’ll need a warehouse or storage facility on site to store it properly, or you run the risk of ending up with old, wet plaster.
“Our clients have been a lot more receptive to delays,” added Huggett. “They accept that because of the pandemic we’re in the middle of so many unknowns, and they understand some deadlines may not happen. We try to advise our clients that contingency is key, and to be patient with the process.”
“Inundated With Enquiries”
The pressure on tradespeople has ramped up this year, impacted by factors including Eastern European construction workers returning to Europe following Brexit and a 20-year high in demand for construction workers, which FMB chief executive Brian Berry has said is putting small businesses under grave pressure.
Combined with price rises and materials shortages, some builders are now spinning more plates than ever before.
(MORE:Find a Builder)
“We’ve had to disappoint people as demand has increased so much”, said Lloyd, who admits his business was particularly affected by a 23% increase in insulation products in April.
“We are inundated with enquiries,” added Huggett. “We have a lot of people who have purchased properties due to the reduction in stamp duty, and due to people seeing the value in outside spaces because of the pandemic. Plus, the property price hike appears to have been the catalyst for more people moving, or spending it on a new extension.”
Huggett too says he is feeling the squeeze of materials costs. “We’re experiencing from a 5% up to 50% increase in some materials, and we can’t continue like that. Specialist timbers and cement and plasters are all restricted, and there are supply issues across the country too.”
Brian Berry, said in July: “While it’s brilliant to see small, local building companies and sole traders bouncing back from the difficulties of 2020, record workloads and enquires are bringing significant challenges.
“An extraordinary 98% of small builders now face rising prices for building materials, with the same number expecting this to continue into the autumn. Half of those who responded to our survey are struggling to hire a carpenter or a bricklayer. Without these fundamental inputs, how can Britain build back better?”
Homebuilding & Renovating Newsletter
Get the latest news, reviews and product advice straight to your inbox.
Jack has worked in journalism for 11 years and is the News Editor for Homebuilding & Renovating, a role he has had since 2019. He strives to break the most relevant and beneficial stories for self builders, extenders and renovators, including the latest news on theconstruction materials shortage和氢加热。2021年,他出现在BBC的The World at One to discuss the government's planning reforms.
He enjoys testing new tools and gadgets, and having bought his first home in 2013, he has renovated every room and recently finished a garden renovation.
Thank you for signing up to Homebuilding. You will receive a verification email shortly.
There was a problem. Please refresh the page and try again.