12 ways to keep your self build budget on track
希望确保自己建立预算tays on target? Our top 12 tips are here to help you plan and organise your finances, as well as offering advice on how to save some pennies
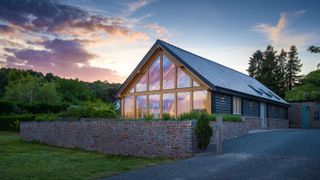
Whatever the shape, size or style of your dream home, a bespokeself buildis likely to represent the biggest shopping trip you’ll ever take.
Whether you’re working with a shoestring budget or a larger sum, it’s important to be realistic about what’s ultimately achievable with the funds you have, in terms of taking materials, labour, permits and fees all into account.
“This will help you stay on track and avoid overspending,” says Harry Reece, managing director atBase Architects. “Careful, considered planning is essential for any self-build project. By forward planning, you can avoid unexpected costs and delays, making the most of your budget.”
If one of your goals is to keep spending to a minimum, there are several smart strategies you can employ to keep costs down. To find out the most effective ways to save money, we spoke to several self-builders to discover their top tips —and we share them here.
1. Fine tune your budget
It’s a given that running your finances effectively is an essential step if you want to keep outgoings to a minimum. Prioritising 'must-have' items over 'nice-to-have' details allows you to direct funds towards areas where your cash adds the most value in terms of achieving your wider aspirations for the project, simultaneously saving money in other areas.
After consulting aquantity surveyorto price up your project, create a spreadsheet that details every item on your self-build shopping list.
“We put all elements of our project into a spending list that included three sections — necessary items, things we’d like to have and luxury aspects,” says Leanne Player, who built a three-bed timber frame house withFrame Technologies.
Any time you’re required to make a financial decision, you can go back to your initial list of components to weigh up what you can afford at each stage, in line with your overall budget.
“I’d recommend splurging on the things you know you want to make a feature of," says Leanne. “For us, this was bifold doors.”
2. Shop around for materials
Take time to track down the best deals for materials and don’t be shy when it comes to thrashing out better prices for products you want — keep your eyes peeled for special discounts and promotions. While shopping around, do your best to maintain a ‘big picture’ view of the overall budget. If you have a limited time to seek out the best bargains, focus on the items that will account for the bigger budgetary costs, such ascheap bricks, rather than smaller items that will only save a few quid.
According to Graham Roberts who worked withWelsh Oak Frameto create a stunning single-storey home, major savings can be made. “I compared prices for big-ticket items such as cement, timber, slates, insulation, scaffolding and windows,” he says. “Merchants often set their own local prices and by shopping around, major savings can be had,” says Graham who saved several thousand pounds on roofing slates by researching different suppliers.
3. Choose an efficient construction method
It’s impossible to put a price on a smooth-running build programme with minimal construction delays.
“In a market that has seen an uplift in labour costs post-Covid, savings on time can bring significant financial benefits,” says Harry from Base Architects.
For Leanne Player, using a prefabricated timber frame where the build components were manufactured offsite contributed to cost savings. “Frame Technologies erected the panels and floor structure within 48 hours and the rest of the frame within seven days,” she says. Reaching wind and watertight so swiftly meant internal trades were able to start promptly, too.
“We were very efficient time-wise, which added to cost savings down the line.”
4. Be flexible with finishes
Taking an adaptive approach to materials and finishes can help you save money as construction progresses.
Hands-on self builder Alison Bunyan worked withMBC Timber Frameto create her one-and-a-half storey home, which is built on aPassivhausstandard raft foundation. Once the superstructure of the house had reached wind and watertight stage, Alison and her husband Gerald decided to reduce the amount of exterior render on the ground floor.
“I had received a quote for this element, which had almost doubled one year later,” says Alison, who decided to install more weatherboarding on all three gable ends to DPC level as an alternative to the render that was originally planned.
“This saved us approximately £6,000, minus the extra larch cladding, which cost £1,700. This £4,300 saving was possible because we didn’t have any labour costs for weatherboarding installation, which we laid ourselves.”
5. Do your own demolition
Before Charlie Mills and his wife Helen could build their three-bed oak frame cottage, they were required to knock down the existing house that sat on their plot.
“By doing thedemolitionwork ourselves, we saved £15,000,” says Charlie, who has plenty of self build experience in his role as managing director atOakwrights.
Typically, it takes four to eight days to knock down a house, depending on the complexity of the job. Before you bring in the wrecking ball, services such as mains water, electricity, gas and sewer connection need to be cut off and capped.
Protective site fencing should be erected, too, and bear in mind that hazardous materials such as asbestos need to be removed by specialists.
Demolition work needs to comply with construction, design and management (CDM) regulations, too, which means the individual acting as main contractor is legally required to prepare a health and safety plan.
6. Become an on-site labourer
Even if you don’t consider yourself particularly handy or skilled in DIY, rolling up your sleeves and supporting trades on site has the potential to save both time and money on labour costs. From prepping areas for professionals to save them time to tidying up at the end of the day, there are usually plenty of jobs you can assist with if you’re on site frequently.
“I soon discovered that helping an expert as a labourer/assistant saved time, money and ensured a quality job,” says Graham Roberts, who helped with everything frombuilding foundationsand installing insulation, to making tea and tidying up. “Just cleaning up after everyone allowed me to recover materials that had been dropped so that they could be reused. This, of course, saved money, too.”
However, if you’re unsure about tackling jobs that involve more technical know-how, it’s best to bring in the professionals to avoid making those costly mistakes.
7. Lay your own gas membrane
Formed from a thin sheet of plastic, this layer forms a protective barrier against harmful ground gases like radon, methane and carbon dioxide. The sheet is laid as part of the foundation of a property and can also act as a damp proof membrane, preventing moisture ingress into the house.
这表你自己可以提供另一个opportunity to claw back some pennies.
“By laying the gas membrane ourselves, we saved £2,000,” says Charlie Mills.
8. Save on staircase design and installation
In many homes, this built-in element affords a fantastic opportunity to make a design statement. Bringing in a designer to craft a bespoke flight for your home can add to costs — it might be that you’re able to do some of the design work yourself when it comes to turning yourstaircase ideasinto a reality.
“I saved several hundreds of pounds on my oak staircase by comparing my own CAD design with two production manufacturers,” says Graham Roberts. "Not only did I save money but I also got earlier delivery by two weeks.”
Charlie Mills and his wife Helen also managed to save £8,000 by sourcing materials and labour independently for their staircase.
9. Get friends and family involved
称在一些倾向于从朋友和家人n be a major advantage when you’re self building — especially from a budgetary cost-saving perspective.
Alison Bunyan made the most of her children’s skills and expertise throughout the project: one son is a plumber, one is an electrician and one is a joiner.
“Our budget did stretch to paying the family for their work on the project, though I have the distinct impression that family rates applied!” says Alison.
Once the house was eventually made fully watertight, Alison’s daughter arranged for her four brothers to join them for a plasterboarding party over the Easter weekend.
“It was all good fun and a great achievement,” says Alison.
According toCheckatrade, installing drywall in an average room across the walls and ceiling could cost around £480 in labour. When you apply this single-room figure to the whole house, the potential cost saving is huge.
10. Use off-the-shelf outbuildings
If your project incorporates a detached garage, carport orgarden office, it’s worth investigating the options for companies with a portfolio of pre-set designs — this has the potential to save you a lot of cash compared to having a tailor made structure designed from scratch.
Some providers operate across the UK, but you might find a better deal with a company that’s based in your nearby area.
“Instead of having a bespoke garage built, we went to a local company that specialises in garages and sheds,” says Alison Bunyan. “They built us a garage on a slab we had prepared, saving us about £7,000. Fortunately, the size we had planning permission for corresponded with one of the sizes they offered.”
11. DIY fit the pipework for underfloor heating
Laying the pipework for a wetunderfloor heatingsystem is a relatively straightforward job if you consider yourself a competent DIYer.
Checkatrade estimates that installation costs for a water-based system sit between £120 and £135/m2 in a new build scenario, so there’s a good possibility for substantial savings to be made if you feel confident enough take on this job yourself.
“For our underfloor heating, we laid all the pipework ourselves. Then, we got the plumber back in once this was complete, to make the connections and sign everything off,” says Leanne Player.
12. Install your own kitchen
A good-looking, practical kitchen doesn’t need to break the bank — high-quality carcasses, cupboard fronts and countertops can be found at DIY outlets for a fraction of the price you’d pay for more upmarket solutions.
Alison Bunyan and Leanne Player both saved money by sourcing and installing their kitchens independently.
“As well as saving on costs associated with installing the kitchen (Checkatrade estimates the average cost of fitting a new kitchen in 2023 is £1,750), we shopped around for the best deal,” says Leanne. “We ended up getting the worktops from a different place to the kitchen and appliances, as we found a better deal elsewhere.”
Alison adopted the same strategy.
“We bought, constructed and installed an excellent-quality Ikea kitchen, and we sourced and installed a quartz worktop from a local company,” she says.
Considersecond hand kitchenstoo — they can offer some amazing savings.
Is an experienced writer specialising in homes and interiors.
Get the Homebuilding & Renovating Newsletter
Bring your dream home to life with expert advice, how-to guides and design inspiration, direct to your inbox.
Rebecca began her journalism career writing for a luxury property magazine in Bangkok, before re-locating to London and becoming a features editor for a self build magazine. She is an experienced homes and interiors journalist and has written for many homes titles including Homebuilding & Renovating, Ideal Home and Period Living.
She has expertise on a wealth of topics — from oak frame homes to kitchen extensions. She has a passion for Victorian architecture; her dream is to extend an 1800s house.
Most Popular
Bring your dream home to life with expert advice, how-to guides and design inspiration, direct to your inbox.
Thank you for signing up to Homebuilding. You will receive a verification email shortly.
There was a problem. Please refresh the page and try again.