How much does external house cladding cost?
Just how much should you expect your house cladding costs to come to? Whether it’s timber, render, stone or composite — the cladding you choose will have an impact on budget and aesthetics
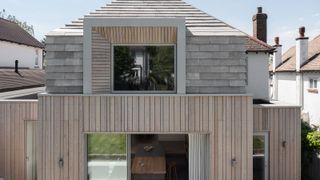
House cladding costs can take up a large part of any build or renovation budget so it is really important that you understand the kind of prices you are likely to be facing.
House claddingis a term used for the process of adding a layer to the outside of a building. It can greatly enhance the appearance of your home and also provide valuable functional purposes — such as protecting your home from the adverse effects of weather and improving insulation. Types of cladding include timber, uPVC, stone, brick, render, composite, fibre cement, metal and tiling.
Here, we look at the various costs involved, together with the factors that influence those costs and any potential issues that can impact costs in the longer term.
What are house cladding costs in 2023?
There are a multitude of different cladding materials and products on the market, with a variety of different qualities, installation methods and costs. The most common materials and average costs are set out in the table below as a guide.
Once you’ve chosen a material type, there’s still a wide range of cost options to consider. You can get a basic cement render from around £10/m2, but expect to pay £30-£60/m2 for monocouche render and £40-70/m2 for the latest self-coloured silicon versions such as K-Rend or Parex.
Timber claddingcosts are equally variable – according to the wood and profile selected – with larch from £15 to £30/m2, western red cedar from £20 to £50/m2 and oak from £25 to £60/m2.
Thermally modified woods (such as Thermowood) can offer good value for money at around £45/m2. They are generally cheaper than most hardwoods but have been heat treated to reduce moisture content, improve longevity, stability and resistance to rot etc.
Cladding (material only) | Average £/m2 |
Render | £22 |
uPVC | £25 |
Composite | £36 |
Timber | £40 |
Fibre cement | £42 |
Stone | £55 |
What is the cheapest external cladding material?
Softwood timber is one of the cheapest cladding materials (from around £8/m2). However, this price will be for rough sawn edged untreated timbers, which will require preparation (in the form of priming/undercoating), finishing (painting or staining depending on your preference) and ongoing maintenance (preservatives, re-painting). Initial material costs can therefore be misleading. Softwood can actually end up being more expensive than hardwood or uPVC cladding, because of its maintenance requirements — something worth bearing in mind when planning out yourcladding ideas.
The most cost-effective cladding option if you’re on a tight budget
is basic white uPVC cladding, as it’s comparatively more durable and lower maintenance over time. Your budget will naturally dictate the options available to you but if you can stretch a little on the material quality, it can cost you less in the long run.
Is render cheaper than cladding?
We’ve already seen that bothhouse rendering和包覆有一个广泛的定价选择ions, so it really depends on the quality of the material you are choosing within each category, and the look you want to capture.
A high-end modern render will be more expensive than if you selected a basic white uPVC cladding. Similarly, a premium hardwood cladding will be far more expensive than a basic render. The final cost of each option will depend on numerous factors that are specific to your home.
Ultimately, when looking at ‘which is cheaper’, you should always consider the overall cost including maintenance over time and not just the initial outlay. Consider the durability of the product — how long will it be before it will need replacing? What guarantees are available for longevity/colourfastness etc? What are the ongoing maintenance requirements, frequency and costs?
Which type of cladding should I choose?
Your choice between render or cladding will be influenced by a number of factors. Each finish can produce entirely different aesthetic results and you need to select the one that works for you and importantly the area your home
is in — it’s always sensible to run your choice past your local planning authority, especially if your choice is dramatically different to the appearance of surrounding homes because you may be required to blend in.
你现有的建筑系统也将factor. Traditional masonry construction ortimber frameare equally suitable for cladding. However, if you are starting with a timber-framed building, rendering is still an option but there will be more work involved in comparison to rendering straight to a masonry construction. So costs will increase in that respect.
Your home’s location and exposure to the elements will also impact your choice of cladding material. For example, a coastal property will require a finish that can withstand corrosion.
How much does cladding installation cost?
Installation costs will vary depending on who will be undertaking the work, the size and nature of the job required, their skills and experience. Your choice of material will also influence the cost of installation.
At the more expensive end, should you choosestone claddingyou can expect to pay around £250/£300 a day for a specialist such as a stonemason. Alternatively, if you’re opting for standard stretcher bond brickwork and engage a general bricklayer, you can expect a lower cost at around £200/day.
For general trades, such as a plasterer, carpenter or general builder, you can expect to pay between £175 and £250/day. Be aware that not all trades have the skills required for all cladding types, so you will need to choose a material in order to identify the correct installer and establish costs.
Doing it yourself is certainly a cost-saving opportunity if you have the right skills and experience.
Which factors could push cladding costs up?
When calculating your likely house cladding costs, there are several factors that will strongly influence what you end up paying. These are:
- Size of house:Inevitably, the larger your home, the higher the cost to clad it. However, you may not want or need to clad your property in its entirety. You could consider a mix of timber/uPVC cladding with other exterior wall materials such as render or stone according to the elevations on show and your preferred design style.
- Complexity of shape of house:A conventional square bungalow built on one level will naturally be cheaper to clad than a complex design with multiple elevations/extensions. More intricate installations will result in higher labour costs. Multiple storeys will also add to scaffolding costs.
- Listed building/protected house types:If your property is listed or within a protected area (National Park/AONB) you will not only have to add the cost of applying for planning permission but the permitted options are likely to be more expensive specialist materials requiring skilled application.
- Preparation required:Removal of your home’s existing finish may reveal additional repair or preparatory works to be undertaken before the cladding works can commence, which can add to the total costs.
- Existing construction system:In some cases, walls will need to be framed with either wood or steel studs to take the cladding. However, for timber-framed buildings you will need additional plywood or other type of board covering to strengthen the frame. This won’t be necessary if your home is of concrete or masonry structure. For timber-framed houses, the walls should also have a breather membrane which prevents moisture penetration, but again, this won’t be necessary if your home is brick built with cavity walls.
- External wall insulation:If you are introducing EWI, this will increase costs. The insulating cladding boards will be fixed to the external walls first, before your chosen finish layer is applied (mineral or synthetic through-colour render or brick slips can also be used). The additional cost should be considered against the improved thermal performance, which is increasingly important with current energy prices.
- Required cladding finish:Always check if your pricing includes any finish required. Basic cement renders will require external masonry paint and your chosen timber may require staining, varnishing etc.
- Access and scaffolding issues:Costs can increase if there are access issues which can lead to double handling of materials. Similarly, scaffolding labour costs can increase if your external walls are close to your boundaries as erecting scaffolding takes longer in narrow spaces.
- Number of window or door openings:This can impact cost in several ways, such as increased material costs due to level of wastage, but also increased labour costs as it will be more time consuming to deal with the intricate finishing required.
- DIY involvement:可以节省成本如果你有经验,排版etent at DIY — basic timber or uPVC solutions are relatively easy to install. Remember that ‘amateur’ work can devalue your home, and if there’s anything wrong with the fitting it will be your responsibility. Note that some of the more specialist cladding products are only available on a ‘supply and fit’ basis in order to obtain the full guarantee offered.
- Skilled labour:If your chosen cladding material requires specialist skills to fit it, this will push up the labour costs. Skilled stonemasons are expensive and becoming harder to source, which drives cost up even further.
- Complexity of patterning:If you’ve chosen a cladding material with pattern options, such as bricks, the more complex the detail, the more time it will take and so labour costs will be higher.
Tim Phillips is a quantity surveyor with almost 30 years of experience across the commercial and residential construction sector.
Get the Homebuilding & Renovating Newsletter
Bring your dream home to life with expert advice, how-to guides and design inspiration, direct to your inbox.
Tim Phillips is an experienced senior quantity surveyor and estimator and has worked in the construction industry for over 35 years. He has worked on many varied projects in this time, for corporates, public bodies and private residential clients, managing multi-million budgets.
For the past 13 years, Tim has worked on a freelance basis, whilst managing his rental property portfolio. He has extensive experience of undertaking his own full-scale house renovations. He is also a speaker and expert at the Homebuilding & Renovating Shows.
Most Popular
Bring your dream home to life with expert advice, how-to guides and design inspiration, direct to your inbox.
Thank you for signing up to Homebuilding. You will receive a verification email shortly.
There was a problem. Please refresh the page and try again.