What is cellulose insulation? It's green but is it any good?
Why is cellulose insulation still shunned by so many people? Made predominantly from paper, cellulose insulation is viewed as an eco-friendly choice, but is not a go-to option. Is it time we woke up to the idea?
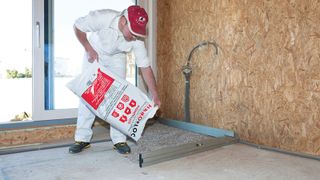
Do you know what cellulose insulation is and how it works? If not, our guide is here to give you everything you need to know in order to decide whether this is the right option for you.
We sort of know instinctively that paper is a good insulator but the idea of using it as ahome insulationwould probably seem unusual to most of us. Cellulose insulation is essentially shredded paper and has been used to keep homes insulated since the 1950s in the US (and 1970s in the UK).
It is arguably considered to be one of, if not the, most environmentally friendly insulation materials available. It is at least as good an insulator as mineral wool or all the natural insulators, so why have we not heard more about it?
What is cellulose insulation?
Typically around 85% of cellulose insulation is recycled paper (mostly newspaper) and cardboard that has been processed to produce a soft fibre. The remaining 15% is formed of organic compounds, which are a necessary addition in order to make
the material unattractive to rodents and pests and fire retardant.
Manufacturing is a fairly simple process as nothing has to be actually ‘made’. The raw material is simply waste paper, which is first shredded then pulverised to reduce it to fibres. During this process, boric acid and ammonium sulphate are typically added. The simplicity of the manufacturing process means it requires very little energy — it actually uses less energy than the manufacture of any other type of insulation material, which has the added benefit of less CO2 being produced. At the end of its life, cellulose insulation is fully biodegradable or can be recovered and used to make other things, like road construction material and building blocks. This makes it a great choice for those looking foreco insulationoptions.
Is cellulose insulation safe?
Obviously paper could present a significant fire risk. The reason why the non-toxic compounds boric acid or ammonia sulphate are added, which make it fire retardant and safe for use around light fixtures. Adding these compounds to the material means it will only smoulder and does not fuel any fire. This is a little likewood fibre insulation.
As with all insulation products, cellulose has to comply with the Euro Class C or British Standards BS 476 or BS 5803 to ensure their fire resistance. In addition, the compounds used to ensure this and its resistance to mould, rodents and other pests, are naturally occurring and harmless to people. So the answer to the question is yes, it is entirely safe.
Can you only use cellulose insulation for walls?
The two main UK manufacturers are Warmcell and Thermofloc, who both offer products for walls and loft. In addition, Thermofloc also produces a pellet-form product with high bulk weight – meaning greater density – which allows it to be used on ground floor construction on top of the concrete slab, under a timber sheet.
For horizontal applications like lofts, loose-fill cellulose is simply tipped out onto the surface and spread by hand to the desired thickness. A simple DIY task. For vertical applications, such as wheninsulating a wall, installation is by one of two methods. It is commonly used in timber frame construction where it can be moistened with a little water and sprayed onto open panels and held in place with a timber sheet and/or plasterboard. Cellulose can absorb up to 30% of its own weight in water without loss of insulation performance, the amount of water used for this method is trivial and it will quickly dry out.
Cellulose can also be blown into closed panels. A hole is cut in the top of the panel, a large diameter hose attached and the fibres literally blown into the panel. Cellulose naturally forms itself around any obstructions – pipes, cables, plug sockets, etc – ensuring there are no cold bridges.
Both methods can be used for sloping roof insulation, with a breathable membrane like Tyvek Housewrap or similar to hold it all in place. The membrane is installed first for blown-in installation or after if the insulation is sprayed in. Both of these methods need specialist equipment and require a thorough understanding of how to do the job. Although the machinery needed is readily available
to hire, this job is usually considered a task for
the professionals.
How much does cellulose insulation cost?
Cellulose insulation is, admittedly, more expensive than more conventional forms of insulation including some othernatural insulationtypes. The typical price is around £9/m² for the material at 100mm thick, compared to £5 to £7/m² for mineral wool. Loose laid in the loft it’s a simple job and can comfortably be done DIY. Blown or sprayed into walls requires specialist equipment and professional skill. That is likely to cost £40 to £70 per hour, depending on where you live.
Is cellulose insulation good?
Cellulose is arguably the most environmentally sensitive insulation material available. It uses waste as its raw material (old newspaper) and thus does not need plants to be grown or animals to be bred specifically for the task. There is almost zero waste material because any that occurs, on site or in the manufacturing plant, can be hoovered up and reused.
R值是衡量材料的抵抗transferring heat, so the higher the number the better. Cellulose insulation has an R value of 2.63m²K/W which is virtually the same as mineral wool, glass fibre and all the other natural insulators.
纤维素绝缘的唯一缺点the price. Factoring in the cost of professional installers, the unit price is comparable to other natural materials but almost twice that of mineral wool or rigid foam. But within the context of an overall build cost, this difference in cost really should not be a deal breaker. If your reason for using a natural insulation material is ‘doing your bit’ for the environment then look no further then cellulose insulation. They don’t, in my opinion, come any better.
What are the pros and cons of cellulose insulation?
All insulation materials have a notional lifespan, in that they degrade, settle or shrink over time, and cellulose is no different to these. Replacing or topping up loft insulation is relatively simple and not unheard of but we seldom feel justified in tearing down a wall to replace the insulation in it. It’s estimated that cellulose insulation is likely to lose up
to 20% of its volume over a period of time due to shrinkage and settlement. This is fairly widely known and a good installer will have the machinery necessary to slightly compact the material allowing 20% extra insulation to be blown in. This deals with the problem effectively but, of course, adds to the cost.
And finally, being soft and fluffy means that it is easy to work with and no need for gloves.
Tim Pullen is an expert in sustainable building methods and home energy efficiency.
Get the Homebuilding & Renovating Newsletter
Bring your dream home to life with expert advice, how-to guides and design inspiration, direct to your inbox.
Tim is an expert in sustainable building methods and energy efficiency in residential homes and writes on the subject for magazines and national newspapers. He is the author ofThe Sustainable Building Bible,Simply Sustainable Homes and Anaerobic Digestion - Making Biogas - Making Energy: The Earthscan Expert Guide.
His interest in renewable energy and sustainability was first inspired by visits to the Royal Festival Hall heat pump and the Edmonton heat-from-waste projects. In 1979
this initial burst of enthusiasm lead to him trying (and failing) to build a biogas digester to convert pig manure into fuel, at a Kent oast-house, his first conversion project.
Moving in 2002 to a small-holding in South Wales, providing as it did access to a wider range of natural resources, fanned his enthusiasm for sustainability. He went on to install renewable technology at the property, including biomass boiler and wind turbine.
He formally ran energy efficiency consultancy WeatherWorks and was a speaker and expert at the Homebuilding & Renovating Shows across the country.
Most Popular
Bring your dream home to life with expert advice, how-to guides and design inspiration, direct to your inbox.
Thank you for signing up to Homebuilding. You will receive a verification email shortly.
There was a problem. Please refresh the page and try again.